In the hierarchy of anecdotal strength, very little beats steel or Kevlar. And while they’re strong, they can’t stretch. Then there’s spider silk.
Sure, a strand might break in a gust of wind or on your unsuspecting face. And a web can be brushed away with a broom. But ounce for ounce, milligram for milligram, almost nothing can compete.
“Spider silk is the benchmark. It’s better than all the manmade materials we have,” says Gregory Holland, a chemistry and biochemistry professor at San Diego State University. “Mother nature makes a lot of interesting materials, but in terms of a combination of strength and toughness, spider silk is the king.”
Researchers have worked for decades to break it down, to understand the genetic makeup. The genes have been sequenced and spider silk has been replicated using goat’s milk, bacteria and even silk worms. But no one knew exactly how the spider spun its silk. Researchers guessed, but they didn’t know for sure. And understanding this bit of biology is one more critical step toward successfully mass producing the silk.
“Trying to understand why Mother Nature does things that we can’t even come close to doing yet is inspiring and challenging,” Holland says. “Cracking this one is sort of like the holy grail of natural material science.”
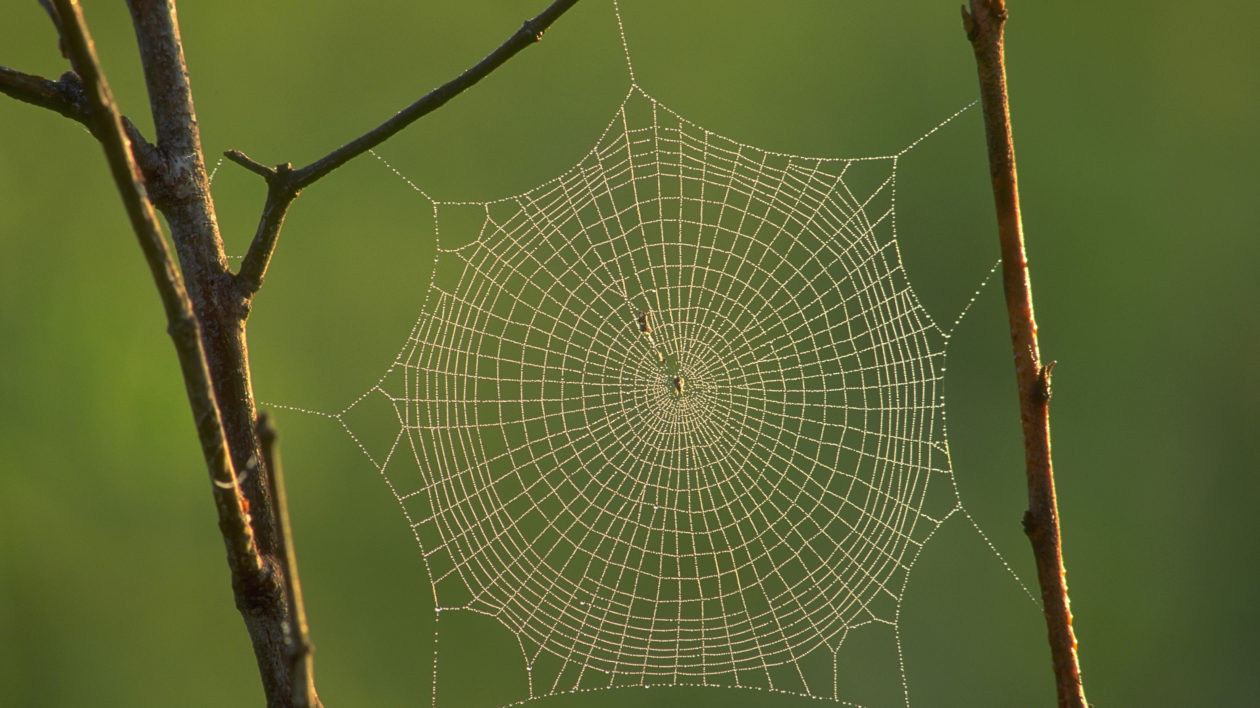
Spider Silk Changes the World?
Ask Holland for the end game, and he’ll tell you it could change the world.
It’s ok if you just raised your eyebrows. But hear him out.
“If you can get spider silk and mass produce it cheaply, you never need plastic again. It’s 100 percent green. It’s made of protein and saltwater,” he says.
“Plastic is cheap. Everything we make is made out of it, we even make cars out of it. But that’s stuff from the ‘50s and ‘60s, the stuff of the next generation will be renewable materials,” Holland continues. “When you think about it broadly from a scientific impact perspective, there are very few things that come into this arena where you really have a chance to make changes that could change the world.”
Randy Lewis, one of the pioneers of spider silk research and Holland’s mentor, colleague and collaborator, believes in the potential of spider silk, but isn’t sure he’d go as far as Holland on replacing plastic or nylon. It’s likely too expensive.
“Right now, my view from 30 years of looking forward, is I don’t see a way to compete with cheap plastic,” Lewis says. “But we can be one of the more high-tech materials in there that have the chemical attributes that other fibers don’t have such as the combination of strength and flex.”
Changing the world or not, both scientists agree continuing to research and produce spider silk could revolutionize human-made materials.
Lewis started working with spiders and on spider silk in 1988 as a professor at the University of Wyoming. In 1990, he isolated the first spider silk gene.
His lab then cloned genes responsible for six types of spider silk – strands used for draglines or the spiral part of the web that have as much stretch as rubber bands or as little as Kevlar. He also was the first to produce spider silk protein in bacteria, goat’s milk and silkworms. The resulting products have been used to coat metals and plastics, even catheters.
“We put antimicrobials on there and prevent bacteria from growing on the catheter itself,” he says.
He also used the genes to grow spider silk in silkworms, recently creating 43 kilometers of fiber to be woven into a defense prototype for the U.S. Navy.
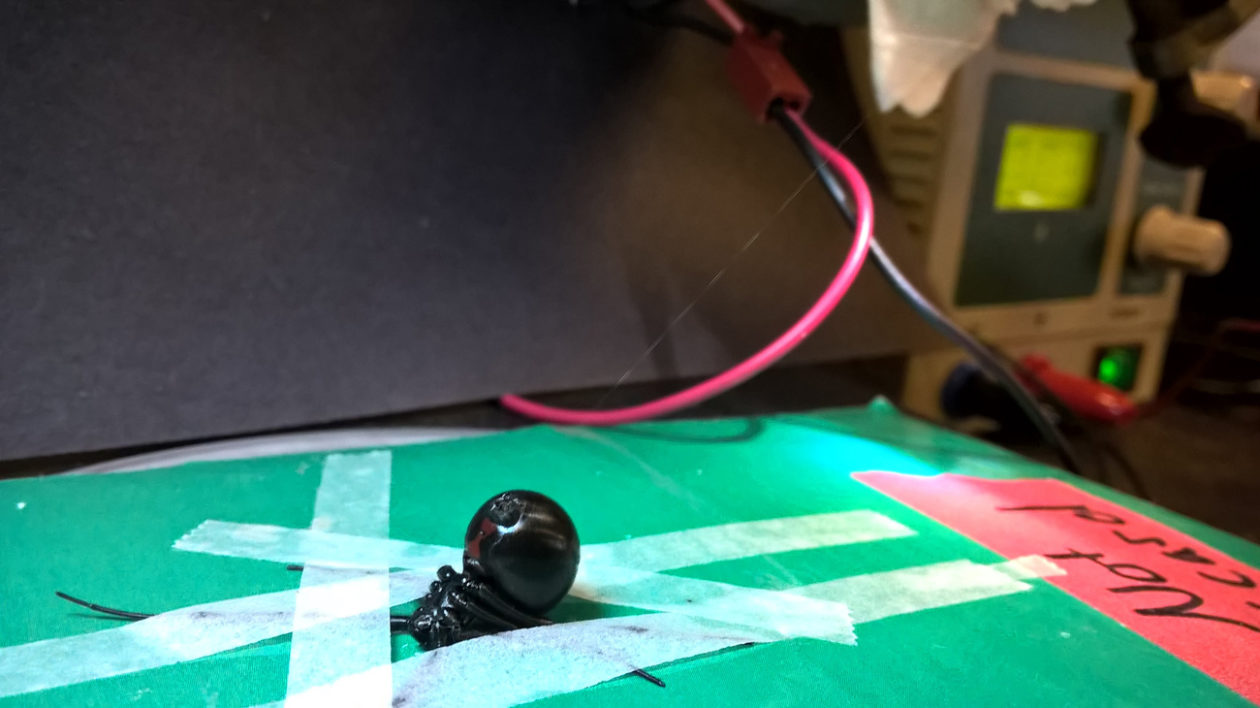
Secrets of the Silk
While Lewis and other labs around the world were working with spider silk and hoping to produce synthetic materials, one component was missing: How the spider arranges the molecules inside of its gland to prevent the silk from forming too early. Researchers knew from Lewis how the genes were sequenced, and knew what the silk looked like under a microscope once produced, but they didn’t know how the proteins were arranged inside those glands.
“The knowledge gap was literally in the middle,” says Nathan C. Gianneschi, Holland’s partner in this study. “What we didn’t understand completely is what goes on at the nanoscale in the silk glands or the spinning duct — the storage, transformation and transportation process involved in proteins becoming fibers.”
That mattered because while researchers could guess how it was all put together in a gland, they didn’t know for sure, and not knowing for sure made replicating it that much harder.
That’s where Holland and Gianneschi came together.
Holland had been working on spider silk using black widows, a venomous spider that instills fear even in most non-arachnophobes. But they’re hearty, available year-round, and “don’t mind living in little cups in the lab as long as you feed them and give them water.”
They also make one of the strongest dragline silks – the strands spiders use to drop down from the ceiling.
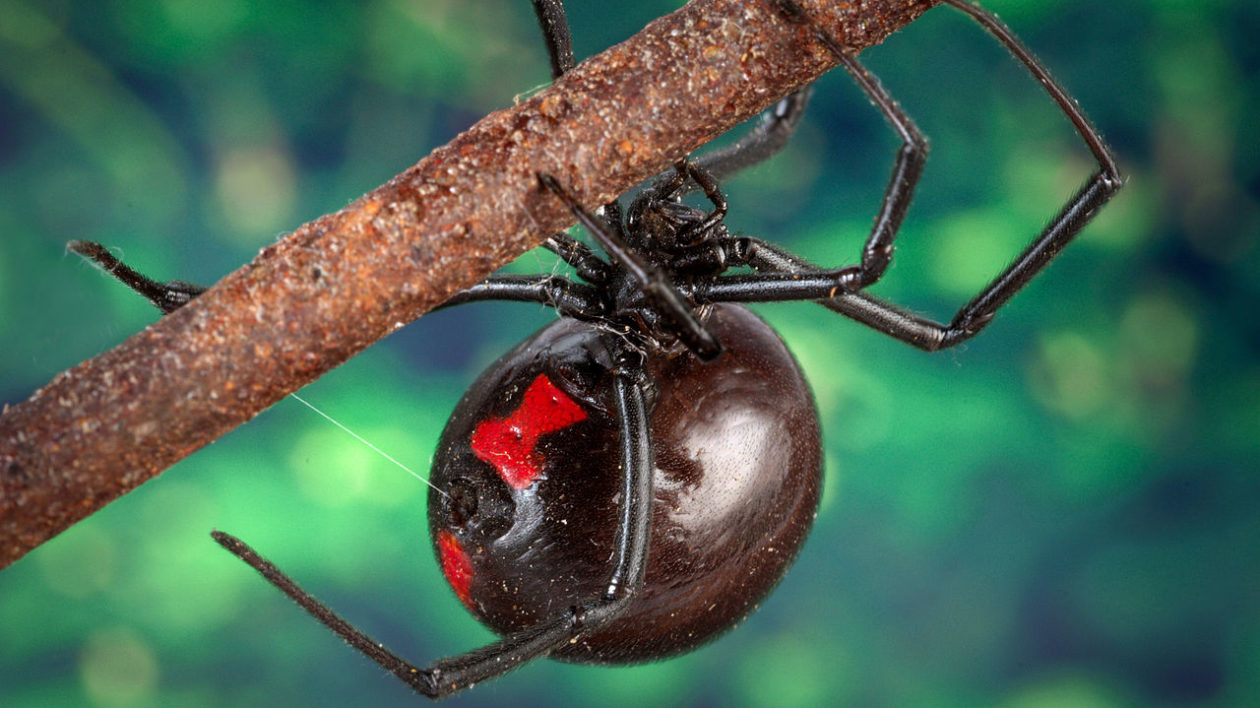
Gianneschi, a chemistry and engineering professor at Northwestern University, was working with equipment so strong and specialized it can essentially take photos of the electrons interacting with the silk proteins by flash freezing the liquid surrounding them.
“And so we took a couple of years with my post-doc at SDSU dissecting spiders and trying to observe what particles were inside the spider before spinning the silk,” he says. “People have made beautiful estimates of what it could look like based on the structure and we essentially photographed it. It’s like postulating there are moons around Jupiter and someone builds a telescope and says yep, you’re right. There are observables and there were limits on what they could observe.”
The research was published in the Proceedings of the National Academy of Sciences in October.
As with many scientific discoveries, solving the puzzle of how the proteins are stored and structured only opens the door to more questions.
“We published this paper that answered a big question or proved a big hypothesis in the field but immediately we have a million other questions,” he says. “It snowballs so quickly.”
They need to know how those stored proteins are influenced by changes in pH, salt or flow, as they assemble into fibers. In really basic terms, Holland and Gianneschi have static pictures of the stored proteins, and now they want to take something akin to a video of how those proteins become silk.
“The next stage is what I really see as the home run,” Holland says.
Lewis will continue in his lab at Utah State University, and is working with a company to expand a pilot project bringing adhesives and composite materials into mass production.
And so from the glands of some of nature’s smallest creatures these researchers hope to change our world.
Umm, I’m sure that you know as a scientist that all crude-oil products such as plastics can be replaced with CRUELTY-FREE and ENVIRONMENTALLY FRIENDLY HEMP!
<3 <3 <3
Very interesting. Think it will be great to use silk from spiders instead of plastic. Our Oceans are full of plastic around the world. Amazing.
I think this is a great idea, we need to make everything with green products and this would be good to eliminate plastics in our world. Anything to reduce what we use would be great for our environment! Now if we could just get rid of this administration and their polluted ideas and clean up our environment would be great too!!!
Fascinating article. If read carefully, one understands that the aim of research is to be able to manufacture spider silk…not to have spider farms/colonies turning the stuff out! Plastic is ruining the earth; in the long run it will not turn out to be cheap.